تنظيف وتطهير وغسيل واعادة تاهيل الخزانات

معمل تكنولاب البهاء جروب
للتحاليل الكيميائية والطبية
والتشخيص بالنظائر المشعة
للمخدرات والهرمونات والسموم
وتحاليل المياه

مجموعة
تكنولاب البهاء جروب
لتصميم محطات الصرف الصناعى والصحى
لمعالجة مياه الصرف الصناعى والصحى
مجموعة تكنولاب البهاء جروب
المكتب الاستشارى العلمى
دراسات علمية كيميائية
معالجة الغلايات وانظمة البخار المكثف
معالجة ابراج التبريد المفتوحة
معالجة الشيللرات
مجموعة تكنولاب البهاء جروب
اسنشاريين
كيميائيين/طبيين/بكترولوجيين
عقيد دكتور
بهاء بدر الدين محمود
رئيس مجلس الادارة
استشاريون متخصصون فى مجال تحاليل وتنقية ومعالجة المياه
متخصصون فى تصنيع وتصميم كيماويات
معالجة الصرف الصناعى والصحى
حسب كل مشكلة كل على حدة
تصنيع وتحضير كيماويات معالجة المياه الصناعية
مؤتمرات/اجتماعات/محاضرات/فريق عمل متميز




صور من وحدات معالجة المياه
technolab el-bahaa groupTECHNOLAB EL-BAHAA GROUP
EGYPT
FOR
WATER
TREATMENT/PURIFICATION/ANALYSIS
CONSULTANTS
CHEMIST/PHYSICS/MICROBIOLIGIST
INDUSTRIAL WATER
WASTE WATER
DRINKING WATER
TANKS CLEANING
CHAIRMAN
COLONEL.DR
BAHAA BADR EL-DIN
0117156569
0129834104
0163793775
0174041455
تصميم وانشاء محطات صرف صناعى/waste water treatment plant design
technolab el-bahaa group
egypt
We are a consultants in water treatment with our chemicals as:-
Boiler water treatment chemicals
Condensated steam treatment chemicals
Oxygen scavenger treatment chemicals
Ph-adjustment treatment chemicals
Antiscale treatment chemicals
Anticorrosion treatment chemicals
Open cooling tower treatment chemicals
Chillers treatment chemicals
Waste water treatment chemicals
Drinking water purification chemicals
Swimming pool treatment chemicals
Fuel oil improver(mazote/solar/benzene)
technolab el-bahaa group
egypt
We are consultants in extraction ,analysis and trading the raw materials of mines as:-
Rock phosphate
32%-30%-28%-25%
Kaolin
Quartez-silica
Talcum
Feldspae(potash-sodumic)
Silica sand
Silica fume
Iron oxid ore
Manganese oxid
Cement(42.5%-32.5%)
Ferro manganese
Ferro manganese high carbon
technolab el-bahaa group
web sites
e-mails
water treatment unit design
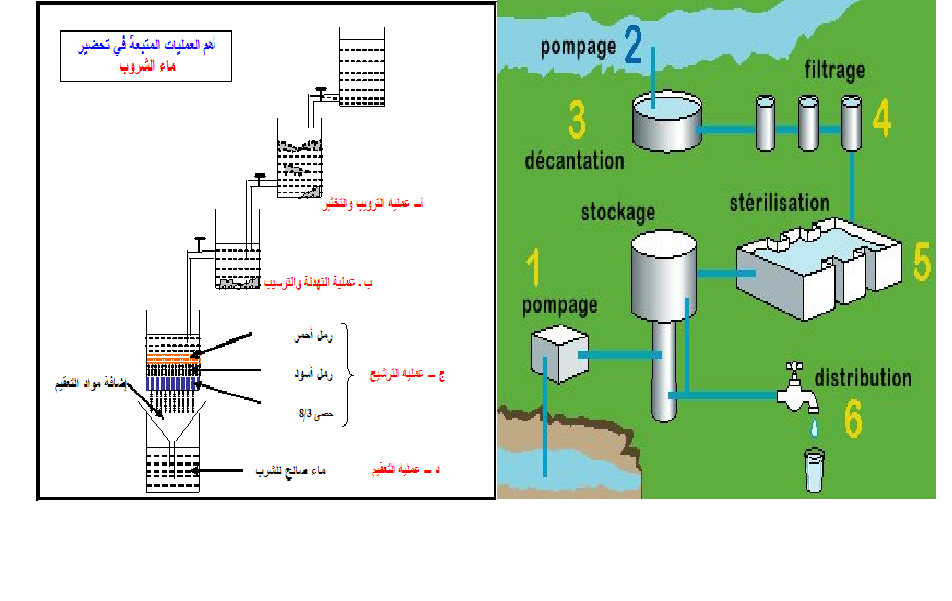
وكلاء لشركات تركية وصينية لتوريد وتركيب وصيانة الغلايات وملحقاتها
solo agent for turkish and chinese companies for boiler production/manufacture/maintance
وكلاء لشركات تركية وصينية واوروبية لتصنيع وتركيب وصيانة ابراج التبريد المفتوحة

تصميم وتوريد وتركيب الشيللرات
design/production/maintance
chillers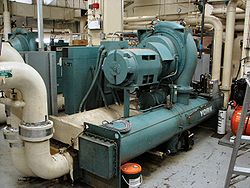
ابراج التبريد المفتوحة
مجموعة تكنولاب البهاء جروب
المكتب الاستشارى العلمى
قطاع توريد خطوط انتاج المصانع
نحن طريقك لاختيار افضل خطوط الانتاج لمصنعكم
سابقة خبرتنا فى اختيار خطوط الانتاج لعملاؤنا
1)خطوط انتاج العصائر الطبيعية والمحفوظة والمربات
2)خطوط انتاج الزيوت الطبيعية والمحفوظة
3)خطوط انتاج اللبن الطبيعى والمحفوظ والمبستر والمجفف والبودرة
4)خطوط تعليب وتغليف الفاكهة والخضروات
5)خطوط انتاج المواسير البلاستيك والبى فى سى والبولى ايثيلين
6)خطوط انتاج التراى كالسيوم فوسفات والحبر الاسود
7)خطوط انتاج الاسفلت بانواعه
محطات معالجة الصرف الصناعى والصحى بالطرق البيولوجية والكيميائية
9)محطات معالجة وتنقية مياه الشرب
10)محطات ازالة ملوحة البحار لاستخدامها فى الشرب والرى
11)الغلايات وخطوط انتاج البخار الساخن المكثف
12)الشيللرات وابراج التبريد المفتوحة وخطوط انتاج البخار البارد المكثف
للاستعلام
مجموعة تكنولاب البهاء جروب
0117156569
0129834104
0163793775
القاهرة-شارع صلاح سالم-عمارات العبور-عمارة 17 ب
فلا تر رملية/كربونية/زلطيه/حديدية

وحدات سوفتنر لازالة عسر المياه
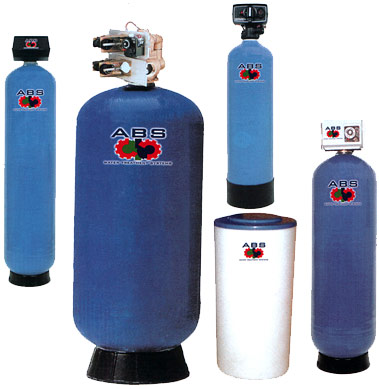
مواصفات مياه الشرب
Drinking water
acceptable
values
50 | colour |
acceptable | Taste |
nil | Odour |
6.5-9.2 | ph |
1 mg/dl | pb |
5 mg/dl | as |
50 mg/dl | cn |
10 mg/dl | cd |
0-100mg/dl | hg |
8 mg/dl | f |
45 mg/dl | N02 |
1 mg/dl | Fe |
5 mg/dl | Mn |
5.1 mg/dl | Cu |
200 mg/dl | Ca |
150 mg/dl | Mg |
600 mg/dl | Cl |
400 mg/dl | S04 |
200 mg/dl | Phenol |
15 mg/dl | zn |
الحدود المسموح به
ا لملوثات الصرف الصناعى
بعد المعالجة
Acceptable
values
treated wate water
7-9.5 | ph |
25-37 c | Temp |
40 mg/dl | Suspended solid |
35 mg/dl | bod |
3 mg/dl | Oil & grase |
0.1 mg/dl | hg |
0.02 mg/dl | cd |
0.1 mg/dl | cn |
0.5mg/dl | phenol |
1.5 ds/m | conductivity |
200 mg/dl | na |
120 mg/dl | ca |
56 mg/dl | mg |
30 mg/dl | k |
200 mg/dl | cl |
150 mg/dl | S02 |
0.75 mg/dl | Fe |
0.2 mg/dl | Zn |
0.5 mg/dl | Cu |
0.03 mg/dl | Ni |
0.09 mg/dl | Cr |
0.53 mg/dl | لb |
0.15 mg/dl | pb |
محطات تحلية مياه البحر بطريقة التقطير الومضى على مراحل
MSF+3.jpg (image)محطات التقطير الومضى لتحلية مياه البحر2![[MSF+3.jpg]](https://2img.net/h/4.bp.blogspot.com/_SynCnHGx75g/Shl2T3oVhsI/AAAAAAAAAEY/_7oem5pvQ3I/s1600/MSF%2B3.jpg)
some of types of tanks we services
انواع الخزانات التى يتم تنظيفها
ASME Specification Tanks
Fuel Tanks
Storage Tanks
Custom Tanks
Plastic Tanks
Tank Cleaning Equipment
Double Wall Tanks
Septic Tanks
Water Storage Tanks
Fiberglass Reinforced Plastic Tanks
Stainless Steel Tanks
Custom / Septic
مراحل المعالجة الاولية والثانوية والمتقدمة للصرف الصناعى

صور مختلفة
من وحدات وخزانات معالجة الصرف الصناعى
التى تم تصميمها وتركيبها من قبل المجموعة

صور
من خزانات الترسيب الكيميائى والفيزيائى
لوحدات معالجة الصرف الصناعى
المصممة من قبل المحموعة
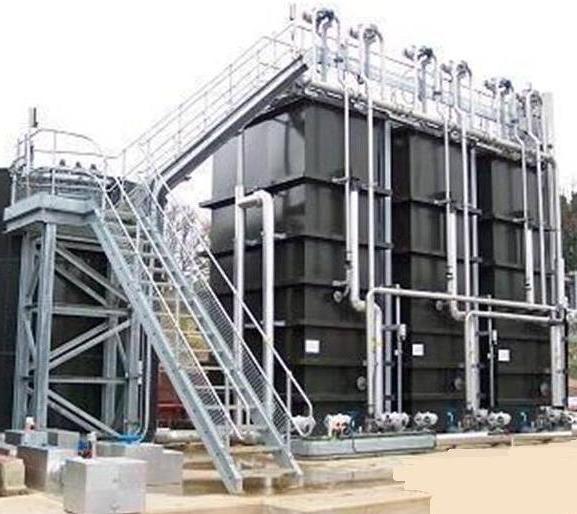

technolab el-bahaa group
technolab el-bahaa group
technolab el-bahaa group
technolab el-bahaa group
technolab el-bahaa group
technolab el-bahaa group
technolab el-bahaa group
technolab el-bahaa group
technolab el-bahaa group
technolab el-bahaa groupمياه رادياتير اخضر اللون
بريستول تو ايه
انتاج شركة بريستول تو ايه - دمياط الجديدة
مجموعة تكنولاب البهاء جروب
اسطمبات عبوات منتجات شركة بريستول تو ايه-دمياط الجديدة
مياه رادياتير خضراء فوسفورية
من انتاج شركة بريستول تو ايه
بترخيص من مجموعة تكنولاب البهاء جروب

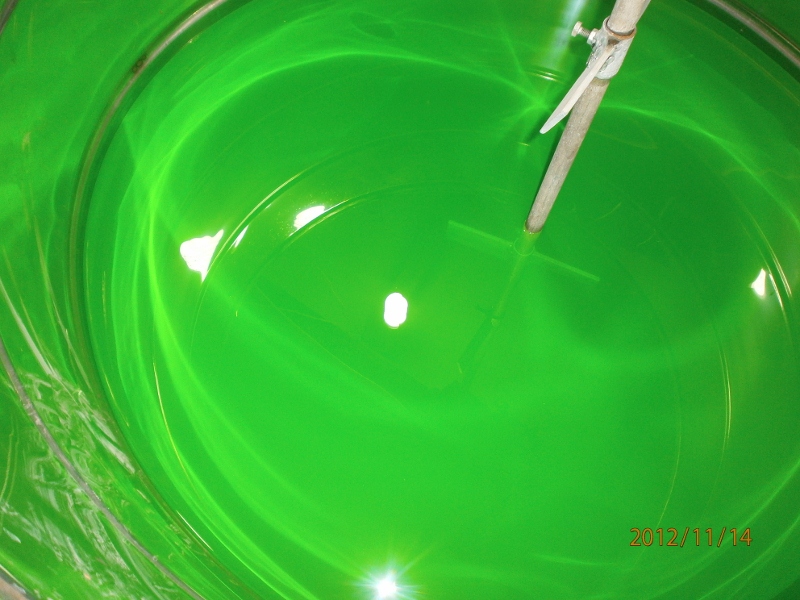

زيت فرامل وباكم
DOT3
