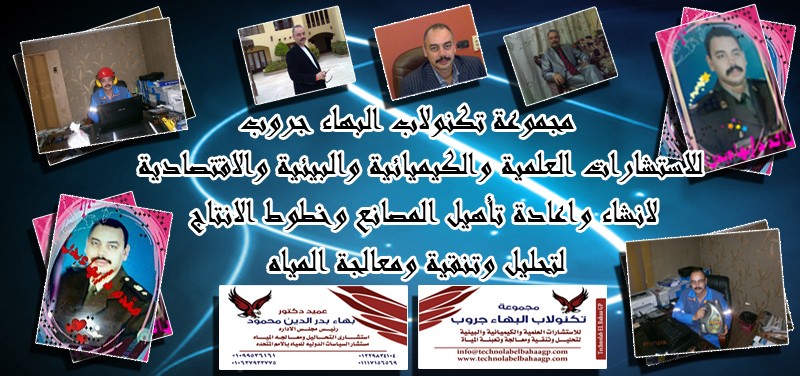
مجموعة تكنولاب البهاء جروب تحاليل وتنقية ومعالجة المياه |
تنظيف وتطهير وغسيل واعادة تاهيل الخزانات

معمل تكنولاب البهاء جروب للتحاليل الكيميائية والطبية والتشخيص بالنظائر المشعة للمخدرات والهرمونات والسموم وتحاليل المياه

مجموعة
تكنولاب البهاء جروب
لتصميم محطات الصرف الصناعى والصحى
لمعالجة مياه الصرف الصناعى والصحى
مجموعة تكنولاب البهاء جروب
المكتب الاستشارى العلمى
دراسات علمية كيميائية
معالجة الغلايات وانظمة البخار المكثف
معالجة ابراج التبريد المفتوحة
معالجة الشيللرات
مجموعة تكنولاب البهاء جروب
اسنشاريين
كيميائيين/طبيين/بكترولوجيين
عقيد دكتور
بهاء بدر الدين محمود
رئيس مجلس الادارة
استشاريون متخصصون فى مجال تحاليل وتنقية ومعالجة المياه
متخصصون فى تصنيع وتصميم كيماويات
معالجة الصرف الصناعى والصحى
حسب كل مشكلة كل على حدة تصنيع وتحضير كيماويات معالجة المياه الصناعية
مؤتمرات/اجتماعات/محاضرات/فريق عمل متميز     صور من وحدات معالجة المياه
technolab el-bahaa groupTECHNOLAB EL-BAHAA GROUP
EGYPT
FOR
WATER
TREATMENT/PURIFICATION/ANALYSIS
CONSULTANTS
CHEMIST/PHYSICS/MICROBIOLIGIST
INDUSTRIAL WATER
WASTE WATER
DRINKING WATER
TANKS CLEANING
CHAIRMAN
COLONEL.DR
BAHAA BADR EL-DIN
0117156569
0129834104
0163793775
0174041455 تصميم وانشاء محطات صرف صناعى/waste water treatment plant design technolab el-bahaa group egypt We are a consultants in water treatment with our chemicals as:- Boiler water treatment chemicals Condensated steam treatment chemicals Oxygen scavenger treatment chemicals Ph-adjustment treatment chemicals Antiscale treatment chemicals Anticorrosion treatment chemicals Open cooling tower treatment chemicals Chillers treatment chemicals Waste water treatment chemicals Drinking water purification chemicals Swimming pool treatment chemicals Fuel oil improver(mazote/solar/benzene) technolab el-bahaa group
egypt
We are consultants in extraction ,analysis and trading the raw materials of mines as:-
Rock phosphate
32%-30%-28%-25%
Kaolin
Quartez-silica
Talcum
Feldspae(potash-sodumic)
Silica sand
Silica fume
Iron oxid ore
Manganese oxid
Cement(42.5%-32.5%)
Ferro manganese
Ferro manganese high carbon technolab el-bahaa group
web sites
e-mails
water treatment unit design 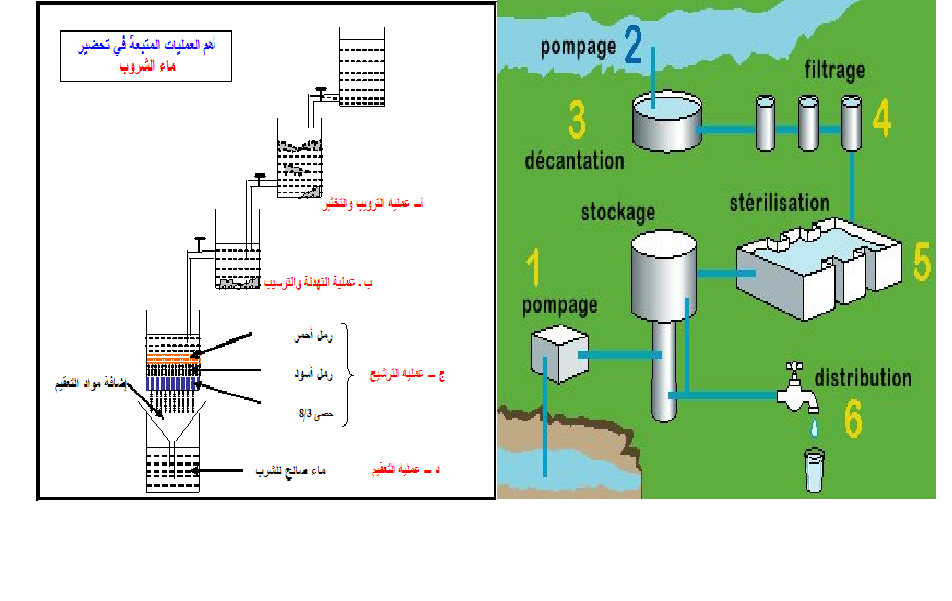
وكلاء لشركات تركية وصينية لتوريد وتركيب وصيانة الغلايات وملحقاتها
solo agent for turkish and chinese companies for boiler production/manufacture/maintance
وكلاء لشركات تركية وصينية واوروبية لتصنيع وتركيب وصيانة ابراج التبريد المفتوحة 
تصميم وتوريد وتركيب الشيللرات
design/production/maintance
chillers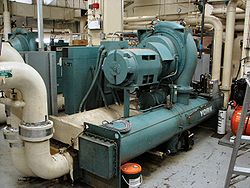 ابراج التبريد المفتوحة مجموعة تكنولاب البهاء جروب
المكتب الاستشارى العلمى
قطاع توريد خطوط انتاج المصانع
نحن طريقك لاختيار افضل خطوط الانتاج لمصنعكم
سابقة خبرتنا فى اختيار خطوط الانتاج لعملاؤنا
1)خطوط انتاج العصائر الطبيعية والمحفوظة والمربات
2)خطوط انتاج الزيوت الطبيعية والمحفوظة
3)خطوط انتاج اللبن الطبيعى والمحفوظ والمبستر والمجفف والبودرة
4)خطوط تعليب وتغليف الفاكهة والخضروات
5)خطوط انتاج المواسير البلاستيك والبى فى سى والبولى ايثيلين
6)خطوط انتاج التراى كالسيوم فوسفات والحبر الاسود
7)خطوط انتاج الاسفلت بانواعه
محطات معالجة الصرف الصناعى والصحى بالطرق البيولوجية والكيميائية
9)محطات معالجة وتنقية مياه الشرب
10)محطات ازالة ملوحة البحار لاستخدامها فى الشرب والرى
11)الغلايات وخطوط انتاج البخار الساخن المكثف
12)الشيللرات وابراج التبريد المفتوحة وخطوط انتاج البخار البارد المكثف
للاستعلام
مجموعة تكنولاب البهاء جروب
0117156569
0129834104
0163793775
القاهرة-شارع صلاح سالم-عمارات العبور-عمارة 17 ب فلا تر رملية/كربونية/زلطيه/حديدية

وحدات سوفتنر لازالة عسر المياه
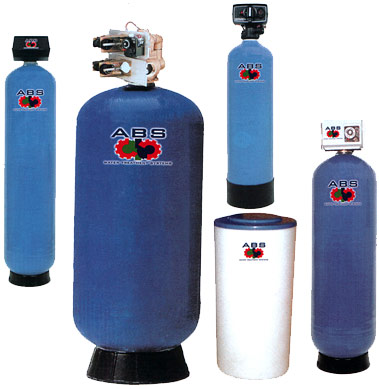
مواصفات مياه الشرب
Drinking water
acceptable
values
50 | colour | acceptable | Taste | nil | Odour | 6.5-9.2 | ph |
1 mg/dl | pb | 5 mg/dl | as | 50 mg/dl | cn | 10 mg/dl | cd | 0-100mg/dl | hg | 8 mg/dl | f | 45 mg/dl | N02 | 1 mg/dl | Fe | 5 mg/dl | Mn | 5.1 mg/dl | Cu | 200 mg/dl | Ca | 150 mg/dl | Mg | 600 mg/dl | Cl | 400 mg/dl | S04 | 200 mg/dl | Phenol | 15 mg/dl | zn |
الحدود المسموح به
ا لملوثات الصرف الصناعى
بعد المعالجة
Acceptable
values
treated wate water
7-9.5 | ph | 25-37 c | Temp | 40 mg/dl | Suspended solid | 35 mg/dl | bod | 3 mg/dl | Oil & grase | 0.1 mg/dl | hg | 0.02 mg/dl | cd | 0.1 mg/dl | cn | 0.5mg/dl | phenol | 1.5 ds/m | conductivity | 200 mg/dl | na | 120 mg/dl | ca | 56 mg/dl | mg | 30 mg/dl | k | 200 mg/dl | cl | 150 mg/dl | S02 | 0.75 mg/dl | Fe | 0.2 mg/dl | Zn | 0.5 mg/dl | Cu | 0.03 mg/dl | Ni | 0.09 mg/dl | Cr | 0.53 mg/dl | لb | 0.15 mg/dl | pb |
محطات تحلية مياه البحر بطريقة التقطير الومضى على مراحل MSF+3.jpg (image)محطات التقطير الومضى لتحلية مياه البحر2![[MSF+3.jpg]](https://2img.net/h/4.bp.blogspot.com/_SynCnHGx75g/Shl2T3oVhsI/AAAAAAAAAEY/_7oem5pvQ3I/s1600/MSF%2B3.jpg) some of types of tanks we services
انواع الخزانات التى يتم تنظيفها
ASME Specification Tanks Fuel Tanks Storage Tanks Custom Tanks Plastic Tanks Tank Cleaning Equipment Double Wall Tanks Septic Tanks Water Storage Tanks Fiberglass Reinforced Plastic Tanks Stainless Steel Tanks Custom / Septic
مراحل المعالجة الاولية والثانوية والمتقدمة للصرف الصناعى

صور مختلفة من وحدات وخزانات معالجة الصرف الصناعى التى تم تصميمها وتركيبها من قبل المجموعة

صور من خزانات الترسيب الكيميائى والفيزيائى لوحدات معالجة الصرف الصناعى المصممة من قبل المحموعة
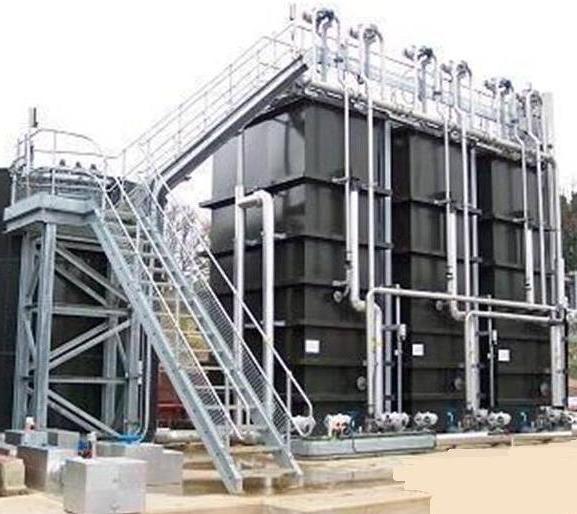
 technolab el-bahaa group
technolab el-bahaa group technolab el-bahaa group technolab el-bahaa group technolab el-bahaa group technolab el-bahaa group technolab el-bahaa group technolab el-bahaa group technolab el-bahaa group technolab el-bahaa groupمياه رادياتير اخضر اللون بريستول تو ايه انتاج شركة بريستول تو ايه - دمياط الجديدة مجموعة تكنولاب البهاء جروب
اسطمبات عبوات منتجات شركة بريستول تو ايه-دمياط الجديدة مياه رادياتير خضراء فوسفورية من انتاج شركة بريستول تو ايه بترخيص من مجموعة تكنولاب البهاء جروب 
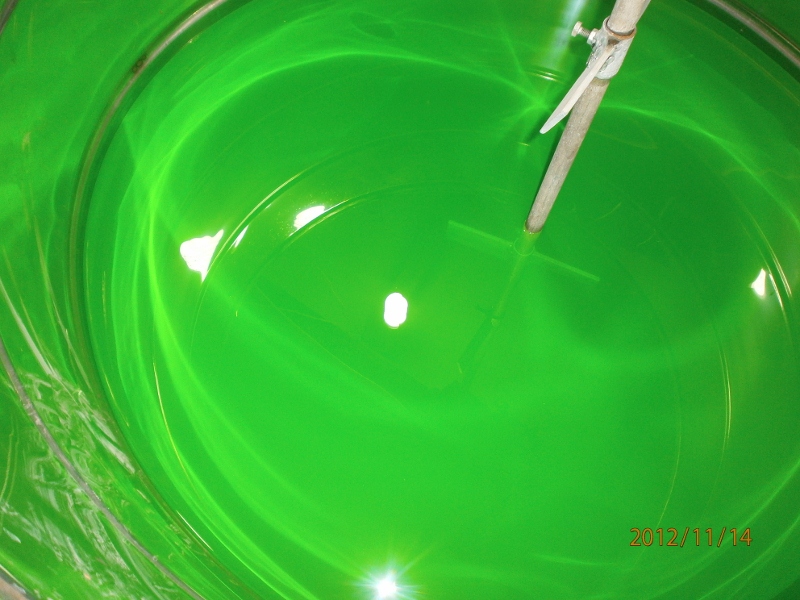

زيت فرامل وباكم DOT3 
|
|
| دراسة جدوى لشركة استثمارية اجنبية لتصنيع الكربون النشط من قش الارز فى مصر(النسخة الانجيليزية) | |
| | كاتب الموضوع | رسالة |
---|
Admin Admin

عدد المساهمات : 3762 تاريخ التسجيل : 15/09/2009 العمر : 57 الموقع : مصر
 | موضوع: دراسة جدوى لشركة استثمارية اجنبية لتصنيع الكربون النشط من قش الارز فى مصر(النسخة الانجيليزية) الأحد مارس 06, 2011 12:33 pm | |
| Activated carbon production from rice hulls
مجموعة تكنولاب البهاء جروب مصر عقيد دكتور بهاء بدر الدين استشارى علمى مقدمة INTRODUCTION
Activated carbon is produced from organic based materials such as coconut shells, palm-kernel shells wood chips, sawdust, corn cobs, seeds etc. The raw material is carbonized to obtain the char or carbonaceous material, which is activated to yield the highly porous final product.
Typically, surface areas ranging from 500- 1400m2/g are obtained for the activated material .
The activated carbon particle has two types of pores existing in it by which adsorption take place.
These are the macropores (>10-1 um) and the micropores (10-3 - 10-1 um) The macropores provide a passageway to the particle's interior and to the micropores but do not contribute substantially to the particle surface area.
The micropores, on the other hand, are responsible for the large surface area of activated carbon particles and are created during the activation process.
It is in the micro pores that adsorption largely takes place. Thus, two main parameters are relevant to the performance of the activated carbon namely the surface area and the pore volume or structure.
The pore volume limits the size of the molecules that can be adsorbed whilst the surface area limits the amount of material which can be adsorbed, assuming a suitable molecular size.
Various methods are available for the activation process but the most widely used are the treatment of the carbonaceous material with oxidizing gases such as air, steam or carbon dioxide and the carbonization of the raw materials in the presence of chemical agents such as Zinc chloride, Magnesium chloride, Calcium chloride or Phosphoric acid.
The carbonized material is treated with oxidizing gas in a furnace or retort at 800-10000C under conditions that permit removal of nearly all the adsorbed hydrocarbons and some of the carbon to increase the surface area.
Chemical treatment activation proceeds under conditions that prevent the deposition of hydrocarbons on the surface.
The raw material is mixed with the chemical agent, dried and calcined at temperatures up to 9000C.
Other methods such as activation of the carbonaceous materials or chars mixed with Potassium hydroxide hydrate as activating chemical , treatment of char with sulphur vapour at elevated temperatures and subsequent desulphurisation with hydrogen and activation in an inert atmosphere under reduced pressure without the use of any chemical activator, are reported.
Treatment of charcoal and carbon black with oxidizing solutions such as nitric acid or a mixture of nitric and sulphuric acidalso increase the surface area as well as introduce acidic oxides (carboxylic, phenolic and quinonic) to the carbon surface.
Activated carbon has several important uses including solution purification such as in the clean-up of cane, beet and corn-sugar solutions, removal of tastes and odours from domestic and industrial water supplies, vegetable and animal fats and oils, alcoholic beverages, chemicals and pharmaceuticals and in waste water treatment. It also finds use in purification of gases, liquid phase recovery and separation processes as well as its use as catalyst and catalyst supports.
For liquid purification or decolorising purposes, it is normally used in the powder form whilst for vapour or gas adsorption, it is used in the form of hard granules.
Liquid phase adsorption or decolorising activated carbons are usually light, fluffy powders produced from low-density material such as sawdust or peat.
Gas phase adsorption activated carbons are hard, dense granular materials produced from high-density raw materials such as coconut shells, palm kernel shells, coal or coke.
PROCESS FLOW DIAGRAM AND EQUIPMENT FABRICATION
The process being developed at the Institute of Industrial Research for activated carbon production is shown in the flow diagram, The preparation of raw materials involves sorting out of dirt or separation of shells from husk in case of coconut and crushing of material to suitable size.
The crushed material is dried to remove moisture. The moisture content of the raw material is an important parameter. If the moisture content is about 20%, the water driven off during the early stages of pyrolysis or carbonisation, reacts with off-gases or impedes their removal.
This allows the off-gases to crack and restrict micropores openings in the product.
The Carbonisation or Pyrolysis Unit is being designed to make provision for collection of the distillate material which contains three main components:
•Condensable gases which yield tar. •Non-condensable gases of high calorific value and which can be used to supplement fuel for heating. •Aqueous phase containing pyrogenic acids.
The carbonised material may further be crushed to size, where necessary, before activation. The activation system consists of a boiler unit to generate steam and a furnace containing the activating stainless steel chamber.
The activation shall be carried out under fluidised bed conditions to facilitate uniform heat distribution and uniform gassolid contact.
The steam activation reaction produces gases such as H2, CO and C02.
The hydrogen and carbon monoxide content of this gas mixture can be burnt in an auxiliary burner to provide supplementary heat for the boiler or for the carbonisation process.
The carbonised product, shall be ground into powder of specified mesh size for liquid phase or decolorising carbons.
In the case of gas phase adsorbing carbons, the granular material shall be ground by tumbling with grit or using any other suitable technique, so as to smooth sharp edges that might abrade into powder during use.
CONCLUSION
There are potential raw material resources for the production of activated carbon to meet local industrial needs.
In addition to the identified raw materials coconut shells, palm kernel shells and sawdust, other raw materials such as corncobs, rice hulls and vegetable wastes can also be used to produce activated carbon.
Besides the gold mining industries, the breweries and soft drink industries that currently use activated carbon, other potential users such as corncobs, rice hulls and vegetable wastes can also be used to produce activated carbon.
Besides the Gold mining industries, the breweries and soft drink industries that currently use activated carbon, other potential users such as the textile industries, soap manufacturing industries, vegetable oil nulls and the Water and Sewerage Corporation can also be sensitised to use this commodity thereby creating more market for the product.
عدل سابقا من قبل Admin في الجمعة مارس 11, 2011 12:53 am عدل 1 مرات | |
|  | | Admin Admin

عدد المساهمات : 3762 تاريخ التسجيل : 15/09/2009 العمر : 57 الموقع : مصر
 | موضوع: دراسة جدوى لشركة استثمارية اجنبية لتصنيع الكربون النشط من قش الارز فى مصر2 الأحد مارس 06, 2011 12:43 pm | |
| . Future of Active Carbon In Egypt
The production of activated carbon from bagasse and rice husk by a single-stage chemical activation method in short retention times (30–60 min) was examined in this study.
The raw materials were subjected to a chemical pretreatment and were fed to the reactor in the form of a paste (75% moisture).
Chemicals examined were ZnCl2, NaOH and H3PO4, for temperatures of 600, 700 and 800 °C.
Of the three chemical reagents under evaluation only ZnCl2 produced activated carbons with high surface areas.
BET surface areas for rice husk were up to 750 m2/g for 1:1 ZnCl2:rice husk ratio.
BET surface areas for bagasse were up to 674 m2/g for 0.75:1 ZnCl2:bagasse ratio.
Results were compared to regular two-stage physical activation methods.
Target /Costumers Target /Product /New Market/ Opportunities .Water purifications use up to 2000 Tons/year •Sugar Processing Factories use up to 2000 Tons/year • The two most widely used products in both applications are: .Aquasorb1000 & Aquasorb2000 •The specs for them are available • Technology for recharging Activated Carbon •Industrial Gas Waste Management •Providing odorless & 2. Industries • Water Treatment Companies
Reference info of activated carbon Raw materials for production of activated carbon
Activated carbons can be obtained from various carbon containing raw materials, including wood, coal andbrown coal, etc. In production of activated carbons, coal, coconut shells and wood serve most of all as raw materials
Activated carbon is an adsorbent
The adsorbent’s qualities depend on surface area Pores sizes Pores distribution structure
The adsorbed substance is the substance that should be adsorbed (removed from water). It is very important to know exactly the characteristics of adsorbed substance, as it possible to find the size and molecular structure of the substance being absorbed. There are three reasons to learn the size of molecules; growth of molecules causes drop in solubility; growth of molecules caused draw in adsorptionas molecules cannot penetrate in the adsorbent’s pores; the bigger the molecules are the more time it takes for them to penetrate into pores As a rule activated carbon is applied in three forms. PowderAC (PAC),Granulated AC (GAC),Compressed AC (CAC). PAC consists mainly of particles smaller than 80 mesh (mesh – is a cell, 80 mesh corresponds to diameter of 0,177 mm) and is used mainly for refinement of liquids inbakery PAC is mixed with water after adsorption of mixtures it goes through mechanical filter or is precipitated. GAC is mainly formed from big particles of coal 50 mesh (0,297 mm) and used for refinement of liquids (water and liquid products) and gases. Sometimes used GAC (for some applications) can be reactivated and used again. Drum-like CAC grains are used for refinement of gases as catalysts and in recovery of gold Application of CAC is similar to that of GAC. CAC can also be reactivated and used again
Production of active carbon and its application
First of all carbon-containing raw materials are subjected to carbonization, i.e. kilning at high temperature, inert atmospherewith no air access. However, the resultant carbonate has pure adsorption qualities, as it is of small size. That’s why the carbonate is subjected to activation to receive specific structure and to improve adsorption properties.
Saw dust is the best material for production of activated carbon.
To obtain 5-6 tons/day it is required to have 50-52m3 of sawdust/day or 1400-1500 m3/month, thickness of the fraction10-80 mm, ash content:≤2%, moisture - 30%. Fir and pine sawdust is preferable.
For high quality it is better to use brown coal and high-moor peat, the quality of carbon made of low-moor peat, shredded stalks of straw, corn, reeds etc is lower .
It is more difficult to use black coal, as it becomes fluid as the temperature reaches 450 C, so its caking and further coking intsted of activation take place, so the whole process should be premanently supervised .
Activation
There are two methods of coal activation
The first method -treatment withwater vapor. We make the equipment that activated coal by water vapors. Water vapor activation is performed at temp. of 800-1000 C, under thorough control, causing chemical reaction between vapor and coal. This results in the developed pores structure and in increase of internal surface of coal. Using such a process it is possible to obtain coal possessing various adsorption properties. Activation by water vapor allows to obtain carbon with internal surface up to 1500m2/gr. Owing to such surface area activated carbons can display brilliant adsorbents qualities. Nevertheless, only part of this surface area is good for adsorption because large molecules of adsorped substances cannot penetrate into small pores.
The second method is activation of coal by special chemical agents. This method is muhc more expensive.
Activating part Carbon containing substances are activated by high-temperature vapor (800-1000°C) or dehydrating chemicals. Raw materials Additive, no less than required by PR China standards Molecular formula Standards Phosphoric acid 1% - 900 kg H3PO4 GB2091—80 Sulphuric acid 1% - 900 kg H2SO4 GB625—89 Hydrochloric acid 1% - 900 kg HCL GB622—89 Water 40 tons/1 ton of coal H2O
Chemical activation Chemical activation consists in heating initial materials to 400-500°C in presence of strong chemical dewatering agent (phosphoric acid, zinc chloride etc) After that some materials are subjected to acid washing. Acid washing eliminates metals, ash and other water-soluble substances (such as silicon) that can be washed out during operations
Pores structure
There are three types of pores in active carbons, namely, macropores, transition pores and micropores, these types differ in sorption mechanisms of vapors and gases.
Mactopores are the largest pores. They have avary highupper limit of radius of curvature (about 2000nm), lower limit - about 100 nm. Capillar condensation of vapors do not fill them.Specific volume of macropores is the range of 0,2—0,8 cm3/g, specific surface is 0,5—2 м2/g.
Thus, adsorption onthe surface of macroporesisof no practical interest. Their surface is equipotent to that if non-porous carbon sorbent with similar chemical nature, whereas the pores themselves play the role of channels for penetration of substances inside sorbent .
Transientpores are less than macropores, their curvature is inthe range of 1.5 -100 nm, i.e. it is much larger,than the size of the adsorbed molecules. Specific volume of the transient pores is rather small - 0.02 - 0.10 cm3/g, specific surface - 20 -70 m2/g. Capillar consensation of vapors can fill these pores. At concentrations lower than that of corresponding capillar condemsation, the vapors absorption cab take place .
Micropores are the smallest pores of active carbons with radius of less than 1.5 nm, the sizes of pores are comparable with those of the molecules adsorbed. As differs from the two first types of pores, inmicropores al thepores volumes is the space with adsorption field, therefore any ideaof layer-by-layer filling and of the surface of microporesloses any sense. Specific volume of micropores of active carbons is 0,20—0,60 cm3/g. Thus micropores play the most important part in adsorption .
Field of use of activated carbons
Chemistry: Refinement of organic acids Adsorption of organic compounds from solutions Recuperation of organic solvents Adsorption of vapors and gases of organic substances Refinement of mineral oils Refinements of electrolytes, production of galvanics Production of electrodes Palladium catalyst support Vinyl-chloride synthesis catalyst’s support Vinyl-acetate synthesis catalyst’s support
Food industry: Refinement of liquors Decoloration of sugar syrups Refinement ofstarch-treacle solutions Refinement of xylite and xylitane Production of organic acids (citric acid, lactic acid, ect) Refinement and finishing of vegetable and animal oils and fats Refinement of low alcohol drinks and carbonated drinks Refinement of starch and treacle solutions, glucose, glucose-galactose alcohols, lactuloses Refinement and deodorization of edible oils and fats Production of citric, lactic, propionic etc. organic acids Decoloration of sugar syrups and xylite Production of caramels
Pharmaceutics : Refinemen solutions at production of medical preparations Production of synthetic rubbers and polyvinylchloride resins. Support for production of catalysts Production of bioactive substances Hemosorbent for medical industry Production of antibiotics Production of blood substitutes Production of carbon tablets Production of calcium gluconates Sodium chloride Production of Allohole tablets Production of cerebrolysine Production of heparin
Industrial refining Refinement vapors and gases Sulphur refinement and process liquors refinement in gas recovery and processing. Refinement of solutions, vapors, gases during oil processing Productions of mineral oils, chemical reagents and paint and varnish product Elimination of spills of oil and oil products. Refinement of vapor condensates and boiler waters Refinement of industrial gases and ventilation exhausts Production of glassy products
Fuel and energy industry Refinement of vapor condensate Refinement of circulating waters Sulphur refinement and process liquors refinement in gas recovery and processing. Oil and gas recovering and processing industry: Productions of mineral oils, chemical reagents and paint and varnish products Elimination of spills of oil and oil products.
Metal manufacture Gold extraction from cyanide pulps and other solutions Ore floatation of minerals Extraction of precious metals Environmental protection Preparation of drinkable water Accessories for additionaldrinkable water refinement filters. Refinement of sewage Refinement ofvent exhausts the air of harmful gases. Application of activated carbon in water treatment
مجموعة تكنولاب البهاء جروب مصر عقيد دكتور بهاء بدر الدين استشارى علمى | |
|  | | Admin Admin

عدد المساهمات : 3762 تاريخ التسجيل : 15/09/2009 العمر : 57 الموقع : مصر
 | موضوع: دراسة جدوى لشركة استثمارية اجنبية لتصنيع الكربون النشط من قش الارز فى مصر(النسخة الانجيليزية) الخميس مارس 10, 2011 5:16 am | |
| rice husk pollution problem •Rice husk is one of the most important pollution problems which affect Egypt weather because the farmers shun it burning, leading to a black cloud and in particular, on the Delta and up to the capital. It is possible to take advantage of the agricultural waste and convert it into useful products such as fertilizer, paper, active carbon and other materials useful for the environment.
by colonel.dr bahaa badr sceintific advisor rice husk Rice husk Burning rice husk Rice hus ash (RHF) Carbonized rice husk (CRH)
What is rice husk?
The outermost layer of the paddy grain is the rice husk, also called rice hull. It is separated from the brown rice in rice milling. Burning rice husk produced rice husk ash (RHA), if the burning process is incomplete carbonized rice husk (CRH) is produced.
Importance of rice husk Around 20% of the paddy weight is husk. In 2008 the world paddy production was 661 million tons and consequently 132 million tons of rice husk were also produced. While there are some uses for rice husk it is still often considered a waste product in the rice mill and therfore often either burned in the open or dumped on wasteland. Husk has a high calorific value and therefore can be used as a renewable fuel.
Production of rice husk
Rice husk is produced in the first step in the milling process when the husk is removed form the grain in the husking stage of the rice mill.
Characteristics of rice husk and RHA
Rice husk is difficult to igninte and it does not burn easily with open flame unless air is blown through the husk. It is highly resistant to moisture penetration and fungal decomposition. Husk therefore makes a good insulation material.
Rice husk has a high silica (SiO2) contents which means that it decomposes slowly when brought back to the field. It also makes it a poor foder Handling of rice husk is difficult because it is bulky and dusty
. It has angle of repose is about 40-45° which means that it's flow ability, e.g. in feed hoppers is very poor. Rice husk has low bulk density of only 70-110 kg/m³, 145 kg/m³ when vibrated or 180kg/m³ in form of brickets or pellets. It thus requires large volumes for storage and transport, which makes transport over long distances un-economical. When burned the ash content is 17-26%, a lot higher than fuels (wood 0.2-2%, coal 12.2%). This means when used for energy generation large amounts of ash need to be handled.
Rice husk has a high average calorific value of an 3410 kcal/kg and therefore is a good, renewable energy source.
Because of the high silica contents rice husk is very abrasive and wears conveying elements very quickly.
Rice husk is not an easy fuel. One concern in rice husk firing is the behavior of the ash, i.e., its slagging and fouling tendency caused by a low melting point of the rice husk ash.
Utilization of rice husk and rice husk ash
Rice husk is produced centrally at rice mills and has low moisture content since the paddy is dried to 14% or less before milling.
The disadvantage is that rice husk has very low density and therefore transport over longer distance is expensive. The most obvious use of rice husk is therefore the use as fuel at or close to the rice mill. But rice husk is also used for some non-energy purposes.
Typical uses fo rice huskNon energy applications
Energy generation Combustion Gasification Pyrolysis Incorporation in soil Bio-fertilizer additive Animal husbandry - low quality feed - litter material Sorbent material in environmental remediation Building material with good thermal insulation Pest control agent Heat generation - cook stoves - furnaces for heating the air in rice dryers - brick kilns Gas for cook stoves Syngas for electricity generation In research phase few commercial applications Steam generation for - parboiling - electicity generation from steam turbines - kinetic energy from steam engines Depending on the energy conversion efficiency the final product can be either white rice husk ash or black carbonized rice husk.
Description White, fine structure Contains around 85-90% amorphous silica around 25% of the weight of husk Black, often still in the shape of the husk Depending on the combustion still contains 8-15% carbon
Use Partial cement replacement material for high-strength concrete Steel additive for quality steel or "tundish powder in steel production.
Used in manufacturing of refractory bricks Insulators Activated carbon Soil conditioner for poor soil Carbon sequestration, bio char Charcoal as fuel
Examples for non-energy applications
Use of rice husk in animal husbandry Rice husk is sometimes used as animal feed stuff and as litter material for pet animals . Untreated hull is low in protein and digestible energy. Husk can be pretreated with 12% NaOH to reduce the silica content from 19 to 3-4% to improve digestibility and used as animal feed. Examples for energy applications
Cook stoves Simple rice husk cook stoves are used for a long time in the Greater Mekong Subregion.
The origin of the desing is unkown, some sources mention Cambodia, others Vietnam.
After a Vietnamese scholar had brought a unit from Vietnam for testing to IRRI in the Philippines many national systems and projects have adapted the technology to local conditions and similar stoves can now be found in most Asian countries.
The cook stoves come in different sizes and usually can boil a pot of water in around 10-15 minutes.
The fuel is cheap and the stove itself very inexpensive but the disadvantage i is that the user is exposed to small, silica rich ash particles in the flue gas.
To generate a cleaner flame the cook stove principle was modified into a gasifyer burner that has a clean flame. Commerical applications exist in the Philippines and in India. Rice husk cook stove in Myanmar Process heat generation for rice drying and parboiling Rice husk furnaces for heating the drying air in rice dryers is the most obvious application for using rice husk since the husk is available as waste at the rice mill and drying of paddy is often done by millers. But only recently with increasing fosil fuel prices there has been a major shift away from kerosene towards rice husk furnaces. e. Mechanical power generation
In Myanmar rice husk is still used as fuel for boilers which generate heat for steam engines.
These steam engines, most of them being produced in the beginning of the last century, still power many rice mills in Myanmar though belt transmissions.
While this is old technology we still believe that this is worth mentioning here as an example for sustainably using rice husk as energy source over decades in an environment where many millers are not connected to the electicity grid.
High fuel prices have led more recently to a revival of rice husk gasifiers, partly for electricity generation (see below) but also ain may cases coupled with a modified internal combustion engine that drives power a rice mill through a belt transmission.
Several commercial units were developed in India and expecially in Cambodia rice millers have installed several units with 20-70 kW capacity.
Electricitiy generation
Small scale applictions between 10-200 kW usually use a rice husk gasifyer coupled with a modified internal combustion engine that drives a generator.
Larger commercial power plants using rice husk typically have a capacity of 1-4 MW and consist of an advanced burner, a boiler and a steam turbine coupled with a generator. Several units have been installed worldwide.
Utilization of carbonized rice husk
Studies conducted by (Haefele et al., 2008) indicate that the bio-char produced by small scale energy applications through incomplete combustion, can improve poor soils but may have little effect on fertile soils, but also lower CO2 emissions.
Rice hulls Rice Hulls Another term for rice husks is rice hulls. As far as non-edible properties, rice hulls are probably the most useful part of the plant.
The hull is the strong protective covering of the grains. The hulls are high in lignin and silica, which give them their strength and also make it very useful in a variety of industries. They are a byproduct of processing so they are a very inexpensive material.
They are a good source of fiber and though humans don't eat them, they are not entirely indigestible, making them a great cheap pet food.
Another property of rice hulls is that they are very difficult to burn and let in moisture due to their natural protective qualities. These properties allow rice to act as a great insulator.
Rice hulls are also very useful in the compost industry. Rice hulls are a great example of a way to use every part of the food we farm even if we don't ingest it ourselves.
Rice hulls (or rice husks) are the hard protecting coverings of grains of rice. In addition to protecting rice during the growing season, rice hulls can be put to use as building material, fertilizer, insulation material, or fuel.Contents Production
Rice hulls are the coating for the seeds, or grains, of the rice plant. To protect the seed during the growing season, the hull is made of hard materials, including opaline silica and lignin. The hull is mostly indigestable to humans.
One practice, started in the seventeenth century, to separate the rice from hulls, it to put the whole rice into a pan and throw it into the air while the wind blows.
The hulls are blown away while the rice fell back into the pan. This happens because the hull isn't nearly as dense as the rice. These steps are known as winnowing. During the milling process, the hulls are removed from the grain to create brown rice, the brown rice is then milled further to remove the bran layer to become white rice.
At the processing plant, the rice is cleaned and hulled. At this point, brown rice needs no further processing. If white rice is desired, the brown rice is milled to remove the outer bran layers. Hulling is the process to remove the hull from the kernel. Hulling can be done by hand by rolling or grinding the rough rice between stones. However, more often it is processed at a mill with the help of automated processes.
The process of mechanical hulling
The rough rice is first cleaned by passing through a number of sieves that sift out the debris. Blown air removes top matter.
Once clean, the rice is hulled by a machine that mimics the action of the hand held stones.
The shelling machine loosens the hulls from the rice. About 80-90% of the kernel hulls are removed during this process.
From the shelling machine, the grains and hulls are conveyed to a stone reel that aspirates the waste hulls and moves the kernels to a machine that separates the hulled from the unhulled grains.
By shaking the kernels, the paddy machine forces the heavier unhulled grains to one side of the machine, while the lighter weight rice falls to the other end.
The unhulled grains are then siphoned to another batch of shelling machines to complete the hulling process.
Hulled rice grains are known as brown rice.
Use
A number of rice-producing countries, (e.g. Thailand), are currently conducting research on industrial uses of rice hulls. Some of the current and potential applications are listed below.
Chemistry
Rice hulk can be used to produce mesoporous molecular sieves (e.g., MCM)[1][2], which are applied as catalysts for various chemical reactions, as a support for drug delivery system and as adsorbent in waste water treatment.
Pet food fiber
Rice hulls are the outermost covering of the rice and come as organic rice hulls and natural rice hulls. Rice hulls are an inexpensive byproduct of human food processing, serving as a source of fiber that is considered a filler ingredient in cheap pet foods
Building material
Rice hulls are a class A insulating material because they are difficult to burn and less likely to allow moisture to propagate mold or fungi. It has been found out that when burned, rice hull produces significant amounts of silica. For these reasons it provides excellent thermal insulation.
Pillow stuffing
Rice hulls are used as pillow stuffing. The pillows are loosely stuffed and considered therapeutic as they retain the shape of the head. Fertilizer
Rice hulls are organic material and can be composted. However, their high lignin content can make this a slow process. Sometimes earthworms are used to accelerate the process.
Using vermicomposting techniques, the hulls can be converted to fertilizer in about four months. SiC production Rice hulls are a low-cost material from which silicon carbide "whiskers" can be manufactured. The SiC whiskers are then used to reinforce ceramic cutting tools, increasing their strength tenfold
Fuel
With proper techniques, rice hulls can be burned and used to power steam engines. Some rice mills originally dispose of the hulls in this way Brewing
Rice hulls can be used in brewing beer to increase the lautering ability of a mash. Juice extraction
Rice hulls are used as a "press aid" to improve extraction efficiency of apple pressing.[4]
Rice husk ash
The ash produced after the husks have been burned, (abbreviated to RHA), is high in silica. A number of possible uses are being investigated for this.
These uses include aggregates and fillers for concrete and board production economical substitute for microsilica / silica fumes absorbents for oils and chemicals soil ameliorants as a source of silicon as insulation powder in steel mills as repellents in the form of "vinegar-tar" as a release agent in the ceramics industry as an insulation material for homes and refrigerants
[u]
عدل سابقا من قبل Admin في الجمعة مارس 11, 2011 1:12 am عدل 1 مرات | |
|  | | Admin Admin

عدد المساهمات : 3762 تاريخ التسجيل : 15/09/2009 العمر : 57 الموقع : مصر
 | موضوع: دراسة جدوى لشركة استثمارية اجنبية لتصنيع الكربون النشط من قش الارز فى مصر(النسخة الانجيليزية) الخميس مارس 10, 2011 5:25 am | |
| Activated carbon production. Equipment
Name Specifications Boiler 1 unit.
Standard steam outflow (kg/hr) steam 6 tons/hr Coal gas consumption 14000 m3 \hour Smoke-deflecting pressure. PA 2 800 Smoke-deflecting air volume 21 000 Standard amount of power, MwT 4,2 Operating pressure (MPa) 1.25/0.7 Water supply temperature (оС) 20 Active area of boiler (m2) 7.78 Steam temperature (оС) 194 Heat emission (%) 78/79.92 Heating area(m2) Irradiation 17.6 Heating area(m2) Convection 136.5/165.5 Density of carbon black output (mg/Nm3) <100 Smoke density (Ringelman scale) <1 Heat exchanger Corrugated pipe, high frequency welding Weight of the main unit (т) 34,8 tons Size 10*4,7*4,1 m Production area 50 m2 Air-blower, total pressure, PA 2 036 Air-blower, air volume 9200 Water consumption, hour 8 tons Boiler energy, total 52 kW AIr blower 7,5kW Water pump 7,5 kW Smoke suction device 37 kW Height of vapor lift 160 meters Personnel 1-2
عدل سابقا من قبل Admin في الجمعة مارس 11, 2011 1:19 am عدل 1 مرات | |
|  | | Admin Admin

عدد المساهمات : 3762 تاريخ التسجيل : 15/09/2009 العمر : 57 الموقع : مصر
 | موضوع: دراسة جدوى لشركة استثمارية اجنبية لتصنيع الكربون النشط من قش الارز فى مصر الخميس مارس 10, 2011 5:37 am | |
| Gas holder 1 unit.
Kiln chamber diameter 2000 mm Kiln chamber area in section 3.14 m2 Fuel all types of black coal, brown coal, turf Fuel consumption 600∼1000 kg/hr Volume of air for gasification 2.2∼2.8 Nm3/kgc Required amount of vapor 0.3∼0.5 kg produce itself Volume of gas 2100-2800 Nm3/h Min heat productivity of gas 5052∼6070 KJ/Nm3 Gas pressure at the outlet 1.5 kPA Number of rotation of ash bowl 2.23 m/hour Personnel 3 person/shift Gas consumption for boiler 60% Gas consumption for drying equipment 10% Gas consumption for carbonization stoves 10% Gas consumption for activation stoves 20%
| |
|  | | Admin Admin

عدد المساهمات : 3762 تاريخ التسجيل : 15/09/2009 العمر : 57 الموقع : مصر
 | موضوع: دراسة جدوى لشركة استثمارية اجنبية لتصنيع الكربون النشط من قش الارز فى مصر الخميس مارس 10, 2011 5:40 am | |
| Drying equipment 1 unit.
Volume of the shell 16 m3 Speed of the shell 5.8 rpm Gradient of the shell 3-5% Total power 7.5 kW. Weight 10 tons. Size: 16 m* diameter 1.2 m. Potantial output 6 tons/hour Production area 45 m2 Personnel 3 persons Heat/hr required 275 kcal/hour Dry vapor 500 kg/hr Receives raw materials with moisture contents 40% Final Moisture contents of the materials 4-5%
| |
|  | | Admin Admin

عدد المساهمات : 3762 تاريخ التسجيل : 15/09/2009 العمر : 57 الموقع : مصر
 | موضوع: دراسة جدوى لشركة استثمارية اجنبية لتصنيع الكربون النشط من قش الارز فى مصر الخميس مارس 10, 2011 5:43 am | |
| Product specifications Product diameter : 30 mm-60mm Product density No less than 1.80 gr/cm3 Production area 20 m2. Granule press for production of activated carbon
Productivity 6-8 tons/hr Power 11 kW Outer size 1500*1500*1800mm Weight 1200kg Personnel 1 person Specifications of products Diameter of product : 30 mm-60mm Density of the product No less than 1.40 gr/cm3 Production area 10 m2. Pressure 40 tons SOurce of force Permanent mechanical force
Productivity 30-35 tons/hour Size 3200 *1300*1300 mm. Fraction of the fed raw materials ≤150 mm. gap between two rollers 5-10 mm Rotations of stationary rollers 292 rpm Rotation of adjustable rollers 285 rpm Engine power 6-phases 18.5 kW. Size of rolling drums Ø720 × 500 mm. Weight 3500 kg.
| |
|  | | Admin Admin

عدد المساهمات : 3762 تاريخ التسجيل : 15/09/2009 العمر : 57 الموقع : مصر
 | موضوع: دراسة جدوى لشركة استثمارية اجنبية لتصنيع الكربون النشط من قش الارز فى مصر الخميس مارس 10, 2011 5:46 am | |
| Mixer. Two-shaft mixing machine
Productivity 20-25 m3/hour Size 4500*900*1000 mm Straight angle of the mixing cutter 200-200 Distance between centers of two shafts 360 mm Reverse rotation shaft diameter 420 mm Rotation of shaft 50 rpm Engine power 4-phase, 30 kW Reducer JZQ500-1Z-12.64 Distance between inlet center and outlet center 2000 mm One step of mixing cutter 332 mm Weight 3,2 tons
| |
|  | | Admin Admin

عدد المساهمات : 3762 تاريخ التسجيل : 15/09/2009 العمر : 57 الموقع : مصر
 | موضوع: دراسة جدوى لشركة استثمارية اجنبية لتصنيع الكربون النشط من قش الارز فى مصر الخميس مارس 10, 2011 5:49 am | |
| Elevator
Outer, spherical-shaped bearing UCP311 (2 pcs.) UCK309 (2 pcs.) Size 10*300*24500 Hopper movement speed 1005mm/sec. Bucket 49 pcs. (49*500=24500) Main shaft rotation speed 60*1005/(400*3.14)=48 rpm Engine Y132S-4, 5.5 kW, 1440 rpm Column's gear reducer ZQ350-20-II V-belt B2100 Stoves LU-1000 XS-1 carbonization stove
Specification of stoves 4 units Personnel 1 Production volume 2 m3 Material of the body Alloyed heat-resistant steel Thickness of metal of the body 5 mm Size 2100*3000*2400 mm Productivity 500 kg cycle stove (2 000 kg/day ) Time of wood carbinization cycle 8 hr Time of brown coal carbonization cycle 30 min Time of turf carbonization cycle 1 hr Fuel consumption 25 kg/hr Type of fuel any electric energy demand 1,5 kW Utilization of emitted gases burnt out in closed circulation system Degree of carbonization less than 93% at least 95% Size of raw material granules 30-60 mm Moisture No more than 5 % Type of burner 15×104Kcal/h. Number of burners 4 Max temperature 1 430° Max temperature deviation inside the stove -\+ 3% Temperature mode is adjustable, 3 modes 750, 900 and 1450о С Operating temperature 500о С Weight difference of raw materials and finished activated carbon 3 tons of fuel granules afford 1 ton of carbonized coal Gas consumption during the first hour 100 m3 hour. Gas consumption at further operation 0 m3 operates due to gases emitted at burning of light raw materials fractions. Weight 3000 kg The stove includes : Ventilator Decompression device Exhaust gas utilization equipment Body Door 1 unit 1 unit 1 unit 1 unit 1 unit
| |
|  | | Admin Admin

عدد المساهمات : 3762 تاريخ التسجيل : 15/09/2009 العمر : 57 الموقع : مصر
 | موضوع: دراسة جدوى لشركة استثمارية اجنبية لتصنيع الكربون النشط من قش الارز فى مصر الخميس مارس 10, 2011 5:52 am | |
| LU- 5000 XS-1 activation stove 2 units. Steam consumption for activation of 1 ton of coal 4 tons Burner's type 15*104Kcal/h. Max temperature 1 430о Max temperature deviation inside the stove -\+ 3% Production volume 4 m3 Material of the body Alloyed heat-resistant steel Thickness of metal of the body 5 mm Size 2100*4000*2300 mm Productivity 500 kg cycle (2 000 kg/day) Time of activation cycle of wood granules 4 hr Time of activation of brown coal granules 3 hr 30 min Time of activation of turf granules 4 hours Fuel consumption 25 kg/stove Type of fuel any electric energy demand 5 kW Size of granules 3-6 mm Moisture No more than 40 %, with acidic washing Temperature mode is adjustable 5 modes 450, 750, 900, 1200 and 1450 о С Operating temperature 900о С Weight 5000 kg Number of burners 4 utilization of emitted gases Burned out in closed circulation system Gas consumption during the first hour 100 m3 /hr Gas consumption at further operation 0 m3 operates due to gases emitted at burning of light raw materials fractions. Weight difference of raw materials and finished activated carbon 2,5 tons of carbonized brown coal yield 1 ton of activated carbon . Degree of activation of surface 100% Personnel 1 The stove includes: Ventilator Decompression device Exhaust gas utilization equipment Body Door 1 unit. 1 unit. 1 unit. 1 unit. 1unit. Steam supply system 2 sources Nitriding bath
Size diameter 2,2 m х height 1,8 m Power 1 kW 2 pumps for agressive media х 0,5 kW =1 kW Weight 800 kg Material Stainlee steel Wall thickness 2 mm Conveyor
Belt conveyor for feeding dry materials 5000 mm х 400 mm х 350 mm -5 units. Dry material belt conveyor for carbonization stoves 8000 mm х 400 mm х 350 mm- 4 units. Dry material belt conveyor to activation stoves 5000 mm х 400 mm х 350 mm- 4 units Belt conveyor to convey packed coal for sealing 2500 mm х 400 mm х 350 mm -4 unit. Belt conveyor to convey activated carbon from stoves to packing 6000 mm х700 mm х 3500 mm- 2 units Belt conveyor for large materials return 16 000 mm х700 mm х 3500 mm 2 units. Raw materials feeding belt conveyor 6000 mm х 400 mm х 350 mm-6 units. Total power consumption 3 kW х 27 = 81kW. Total Weight 13 5000 kg Self propelled pnematic lift LCUD-2000\HD
Max lifting height 2500 mm Distance from the load center 600 mm Height of load forks over the earth 100 mm Length of load forks 950 mm Width of load forks 850 mm Min turning radius 1525 mm Size of driving wheel 260 mm Speed of movement at full load 0-6 km/hour Lifting speed at full load > 4.5 m/min Speed control method Non-level MOS speed control system Lifting percentage at full load 5% Battery 6Q-100AH/24V Total power 3.4 kW Power by main unit Drive motor 1.2 kW Lifting motor 2.2 kW Weight 820 kg Height of the frame during retraction 1850 mm Max height during the operation 3100 mm Length of the machine's body 1925mm Total width 950mm Number of workers 1 Max lifting capacity 2000 kg Recommended time of operation 2-8 hrs LSUGHJ-P5W Packing section
the section includes Main weighing and packing unit LSUGHJ-P5W – 1 unit. Belt conveyor 1 unit. Raw materials feeding belt conveyor 1 unit. Air compressor 1 unit Lift type sealing machine 1 unit Main unit's features : Accuracy of weighing ±0.2 – 0.4% Air pressure ≥ 0.36 MPa Method of weighing Electronic meter Frequency/pressure 50 HZ 380 V Total power 7 kW Main weighing and packing unit LSUGHJ-P5W 200 kg Lift type sealing machine 100 kg Belt conveyor 100 kg Raw materials feeding belt conveyor 250 kg Air compressor 100 kg Total weight 750 kg Manufacturing technology raw materials transportation-transfer hopper-automatic weighing, automatic filling-transporation-bag sealing Potantial output 300 packing and sealing operations/hour Bunching attachment 1-25 kg Number of operators 3 persons; 2 for sealing machine,1 for conveyor Production area 20 m2 Size: LSUGHJ-P5W Main weighing and packing machine 1400 mm х 1300 mm х 3000 mm Lift type sealing machine 500*500*1500 mm Air compressor 900 mmх 350 mmх700 mm
| |
|  | | Admin Admin

عدد المساهمات : 3762 تاريخ التسجيل : 15/09/2009 العمر : 57 الموقع : مصر
 | موضوع: دراسة جدوى لشركة استثمارية اجنبية لتصنيع الكربون النشط من قش الارز فى مصر الخميس مارس 10, 2011 5:55 am | |
| Batching device
Productivity 50m3/hr Max diameter of large fraction 60mm Error of weighing ≤2% Hopper's volume 3000 L Number of hoppers 3 units. Volume of weighted substance 1200 L Power of belt conveyor 3kW*4 Weight of the unit 4000kg Outer size 9050*2262*2840 Feeding and clearing of raw materials wheeled or crawled unitsm with electric or diesel motor can be chosen by the customer
Power Power Power Rated speed Max step Max uidle speed у Electric energy consumption Operating shaft speed Operating shaft direction total Power Hydraulic liquid Brand Number of rollers - Drive roller - Upper supporting rollers - Lower sliding rollers Number of crawls Length of crawls : Pressure in the ground Weight Lengthх Height х Width Distance between the wheel's axis WIdth of rut : Clearance : Radius of actvion from the feeding source Max speed Working speed Productivity Speed at working state Speed at non-working state Speed of conveyor/ traction force (km/hour) Reverse movement speed 15 kW 11 kW 5.5 kW 55.16 rpm 1500 Н.m 392 rpm 16-20 kW/hr. 632 rpm clockwise 31,5 kW 120 kg 48 16 unit including 4 units 4 units 8 units 90 - 110 units 388mm 7.74 m. 40.2 Kpa 7800 kg 7500mm х 3300mm х 2300mm 1622mm 1435mm 260mm 25 meters 10 km/hour 50 m/hour 10 tons\hior 5 km/hour. 10 km/hour. Н: 10.45/11768 3.07km\hour Other units Packing of activated carbon Unified 5-25 Conveyors Unified 5-100 Hoppers Unified 5-25 Mixers and attritors Unified 5-25 Packing of granules Unified 5-100 Screens Unified 5-100 Elevators Unified 5-100 Crushers Unified 5-100 Movable lifting units Wheeled or crawled by Customer's choice Is not in the set Complete set To be purchased on the spot assembling reinforcement, entrance cables, stop valves, ventilation . Stove for thermal-acidic treatment of activated carbons
Trademark MEGA POWER Type LU-5000 XS-1 Universal stove Series НP Developer USA and Israel Year of development 2009 Made in China at the developers' enterprices Purpose Obtaining of activated carbon, obtaining of charcoal, obtaining of nitric, noble heavy and rare-earth metals . Steam consumption of acidic mixture supplied via aeration pipes 1 ton/hour. 4 tons for 4 hours Max temperature 1 430°С Max temperature deviation inside the stove -\+ 3% Main operating temperature at carbonization 450 °С Main operating temperature at activation 950 °С Operating temperature at enrichment of metal salts in nitric acid 1350°С Main operating temperature at benefecation of swamp ores, swump-turf ores and other ores in organic medium 1230°С
| |
|  | | Admin Admin

عدد المساهمات : 3762 تاريخ التسجيل : 15/09/2009 العمر : 57 الموقع : مصر
 | موضوع: معدات والات مصنع انتاج الكربون النشط من قشرة وقش الارز الخميس مارس 10, 2011 10:51 am | |
| Activated carbon production. Equipment Boiler Gas holder Drying equipment Fuel granules production press Granule press for production of activated carbon Mixer. Two-shaft mixing machine Elevator Stoves Nitriding bath Conveyor Self propelled pnematic lift LCUD-2000\HD LSUGHJ-P5W Packing section Batching device Feeding and clearing of raw materials Stove for thermal-acidic treatment of activated carbons Other units Packing of activated carbon Conveyors Hoppers Mixers and attritors Packing of granules Screens Elevators Crushers Movable lifting units
[img]  [/img ][img]  [/img ][img]  [/img] | |
|  | | | دراسة جدوى لشركة استثمارية اجنبية لتصنيع الكربون النشط من قش الارز فى مصر(النسخة الانجيليزية) | |
|
مواضيع مماثلة |  |
|
| صلاحيات هذا المنتدى: | لاتستطيع الرد على المواضيع في هذا المنتدى
| |
| |
| |
|